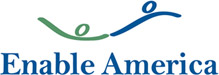
Job Information
St. Jude Medical Cardiology Division Inc. Senior Quality Systems & CAPA Engineer in St. Paul, Minnesota
SENIOR QUALITY SYSTEMS & CAPA ENGINEER St. Jude Medical, an Abbott Labs Co. / St. Paul, MN Responsible for maintaining quality assurance processes and controls related to Corrective Actions and Preventative Actions (CAPAs), investigation principles, and quality system metrics to support Quality System compliance with established standards and agency regulations, including FDA 21 CFR 820, EUMDR (Quality system regulations), and ISO 13485 . Directly support Quality Management System (QMS) audits conducted by regulatory agencies . Lead and conduct root cause investigations and complex CAPA process investigations for the business pertaining to all areas of the Quality System. Support and apply key quality system principles, including Risk management (FMEA, Risk/Design gap analysis), Supplier Quality management (Supplier qualification, APQP/PPQP, Supplier agreements), change management, creation and maintenance of Standard Operating Procedures (SOPs) and Work Instructions, and Validation activities, including Installation Qualification (IQ), Operational Qualification (OP), and Performance Qualification (PQ). Utilize quality related tools and Continuous Improvement principles, including DMAIC (Define, Measure, Analyze, Improve, & Control), Statistical process analysis, 5Whys, Cause and Effect diagrams, Ishikawa 6-M/FishBone Diagrams, and Contradiction Matrices , and other quality principles to drive root cause analysis, resolution planning, and effective CAPA implementation supported by statistical analysis utilizing Minitab, and/or Excel formulation . Mentor CAPA owners on complex CAPA investigations and CAPA principles to ensure compliance to quality system requirements. Apply project management principles to lead Quality Initiatives with cross-functional and cross-site teams to drive improvement. Coordinate effective Quality Metrics, including collection, documentation, and improvement to support monthly and quarterly reviews. Support Quality Metric automation and data integrity activities. Drive implementation and utilization of Quality, Six Sigma, and Lean principles, including 5S and Value Stream Mapping (VSM), and other engineering disciplines, including Geometric Dimension & Tolerancing (GD&T), Gage Repeatability & Reproducibility (Gage R&R) Metrology Calibration, Out of Specification/Calibration, Tooling, Non-Conformance Material Reporting (NCMR) and product disposition , throughout the organization. Create and deliver Quality System training for CAPA, investigation tools and other quality system initiatives. Provide diligent and fact-based communication to Management, peers, and team. Support all Divisional initiatives as identified by divisional management and in support of Quality Management Systems (QMS), Environmental Management Systems (EMS), and other regulatory requirements. Comply with U.S. Food and Drug Administration (FDA) regulations, other regulatory requirements, Company policies, operating procedures, processes, and task assignments. Maintains positive and cooperative communications and collaboration with all levels of employees, customers, contractors, and vendors. Position requires on-site support at three (3) manufacturing facilities located in St. Paul, MN (Ramsey County) and Plymouth, MN (Hennepin County). Master s or foreign equivalent degree in Industrial Engineering or in a related engineering field of study (Will accept a Bachelor s degree with at least 5 years of related progressive professional medical device industry experience in lieu of a Master s degree). Each alternative requirement with an academic or industrial background in: (i) supporting Quality System compliance with established standards and agency regulations, including FDA 21 CFR 820, EUMDR (Quality system regulations), and ISO 13485; (ii) directly supporting Quality Management System (QMS) audits conducted by regulatory agencies; (iii) conducting root cause investigations and complex CAPA process investigations; (iv) key quality sys em principles, including Risk management (FMEA, Risk/Design gap analysis), Supplier Quality management (Supplier qualification, APQP/PPQP, Supplier agreements), change management, creation and maintenance of Standard Operating Procedures (SOPs) and Work Instructions, and Validation activities, including Installation Qualification (IQ), Operational Qualification (OP), and Performance Qualification (PQ); (v) utilizing quality related tools and Continuous Improvement principles, including DMAIC (Define, Measure, Analyze, Improve, & Control), Statistical process analysis, 5Whys, Cause and Effect diagrams, Ishikawa 6-M/FishBone Diagrams, and Contradiction Matrices; (vi) statistical analysis utilizing Minitab, and/or Excel formulation; and (vii) Lean principles, including 5S and Value Stream Mapping (VSM), and other engineering disciplines, including Geometric Dimension & Tolerancing (GD&T), Gage Repeatability & Reproducibility (Gage R&R) Metrology Calibration, Out of Specification/Calibration, Tooling, Non-Conformance Material Reporting (NCMR) and product disposition. Employer will accept any suitable combination of education, training, or experience. An EOE. 40 hrs/wk. Send Resumes to: Abbott Laboratories, Elvia Salazar, Willis Tower, 233 S. Wacker Drive, Floor 25, Dept. 32, Chicago, IL 60606. Refer to ad code: SJM-0009-ES