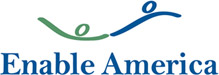
Job Information
American Outdoor Brands Corporation Engineer I in Maryville, Tennessee
Engineer I
The Manufacturing Engineer will develop and implement optimal, cost-effective manufacturing processes and methods in accordance with product specifications and quality standards. The position will recommend and implement improvements to production processes, methods and controls. It will also coordinate manufacturing launch for new or revised products. Priorities include process improvement, problem resolution, project management and employee training.
ESSENTIAL DUTIES AND RESPONSIBILITIES:
When specializing in assembly operations - Essential duties include the following - other duties may be assigned:
Troubleshoot root cause effect relating to product failures and assembly line stoppages.
Use lean concepts to optimize assembly line throughput.
Design, implement and document assembly techniques and equipment that will improve assembly line throughput while maintaining operator safety and product quality.
Implement mistake proof systems in assembly operations to guarantee product quality.
Comply with all with all firearm regulations and traceability.
Participate in testing of products and identifying issues.
Work with operations and engineering to launch new products on time.
When specializing in manufacturing operations -- Essential duties will include the following:
Performs research, design and development of manufacturing processes, including production flow, assembly methods and production equipment.
Must be able to understand and interpret complex part drawings and understand product design intent.
Coordinates the manufacturing launch of new/revised products, including establishing goals, training team members and evaluating results.
Use appropriate project management techniques to insure tools, gauges, fixtures, equipment, routings and CMM/CNC programs are fully defined, documented and implemented.
Designs, develops, tests or sources and cost-justifies various tools, machinery and equipment for recommended manufacturing methods.
Performs product/process analysis for cost reduction, quality improvement and efficiency improvement.
Responsibility to manage and maintain the accuracy of the S&W manufacturing routing database including operation sequence and description , labor hours, set-up and changeover times and machine cycle times as well as appropriate work instructions where applicable.
Must work effectively with external technical support, and continuously train internal staff.
Represents manufacturing on cross-functional teams.
Ability to work in a team environment.
Works with minimal supervision, establish priority and meet scheduled completion dates.
Performs other related duties as assigned
QUALIFICATIONS:
Experience, Competencies and Education
Candidates must have a Bachelor's degree (BSME) or equivalent and 1-5 years' experience in a manufacturing environment (preferably in the firearms industry, and a strong understanding of lean principles)
Experience with PCDMS CMM programming preferred
Experience with Solid Works preferred
Experience in addressing needs and concerns of shop personnel in a manufacturing environment and reflecting a background of good customer service skills
Experience with handling and shooting firearms.
Language Skills
Must have working command of the English language
Must be able to read, write and interpret the English language
Must be able to communicate in English verbally and in writing (verbal instructions, written memos and instructions)
Computer Skills
Proficiency in Microsoft Word, Excel, Access and PowerPoint
SolidWorks and or CAM knowledge a plus
CMM programming & PCDMS a plus
Certificates, Licenses, Registrations
None
TRAINING REQUIREMENTS:
Complete all necessary training as required by assigned department and position
Participate in and follow all company initiatives
Participate in continuous improvement projects (Kaizen events, 5S, etc)
Participate in product testing.
PHYSICAL DEMANDS:
Must be able to sit, stand, walk, climb, bend, stoop, push, pull, carry, reach, twist
Must be able to lift up to 50 pounds
PERSONAL PROTECTIVE EQUIPMENT:
Safety glasses with side shields and hearing protection required when on factory floor
The use of additional personal protective equipment (PPE) may be required when a job task(s) is being completed in or around your assigned department or in another department, this includes safety eyewear, hearing protection, and safety footwear
All employees are required to apply ergonomic correctness to all job tasks
WORK ENVIRONMENT:
Very fast paced and demanding work environment.
Successful candidates spend their majority of time on the shop floor.
Within the Smith & Wesson manufacturing facility, employees may be exposed to manufacturing noise, airborne liquid chemicals, fine particulate dust, ambient temperatures, and industrial lighting
Work environment is similar to most manufacturing operations. May be exposed to excessive noise, temperatures, hazards associated with working around moving machinery, work in confined quarters, exposure to vibrations and shop lighting
Revised 1/3/21
Equal Opportunity Employer Minorities/Women/Protected Veterans/Disabled