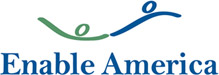
Job Information
Ultralife Corporation Lean Leader in Newark, New York
Ultralife has been located in Newark, NY for over 30 years! We are on Rt. 88 just south of Rt. 31 by the FLCC campus.
Newark is just: 10 minutes from Lyons; 20 minutes from Geneva, Sodus, Farmington, and Macedon; 25 minutes from Canandaigua.
Join our dynamic team and make a significant impact on our company's growth and success. We offer competitive compensation packages, comprehensive benefits, and opportunities for professional development. Apply now to be part of our innovative organization.
The wage range for this role considers the wide range of factors that are considered in making compensation decisions including but not limited to skill sets; experience and training; licensure and certifications; and other business and organizational needs.
Job Summary:
The Lean Leader is primarily responsible for implementation of Lean programs and continuous improvement plans for the B&EP business unit. The Lean Leader will work with cross-functional teams to ensure the successful implementation of Lean and achievement of continuous improvement objectives.
Essential Functions:
Plan and coordinate kaizen events and activities within the business unit to achieve continuous improvement goals.
Implement lean methodologies to promote efficient production processes. Identify opportunities for improvement, develop strategies to address these opportunities, and lead the implementation of these strategies.
Assure complete and accurate tracking of business performance vs. improvement goals.
Track progress of open action items and assure timely closing, escalating as necessary.
Train and coach employees at all levels on lean principles, including value stream mapping, 5S, and Kaizen. Develop a lean training program and promote a culture of continuous improvement.
Link lean activities to the business objectives and develop a transformation plan in collaboration with the management team.
Develop and implement process maps, metrics, and control plans for the key manufacturing processes.
Foster a culture of moving forward in a change environment and continuously assuring buy-in and ownership at all levels.
Act as the plant’s internal 5/6S expert.
Evaluate and rank improvement opportunities versus business ROI or savings to maximize impact to the business.
Education / Training / Skills / Experience:
BS degree desired or 5 years of job-related experience.
Six Sigma green or black belt certified.
Experience working in a manufacturing environment.
Experience leading Lean and continuous improvement efforts.
Strong communication skills
Ability to work effectively with cross-functional teams under limited supervision to meet challenging schedule, technical, and cost objectives.
Detail oriented, organized and ability to work under pressure.
Possess good project management skills to lead teams indirectly to effectively juggle multiple priorities and deliver timely business results.
This job description is intended to convey information essential to understanding the scope of the position described above and it is not intended to be an exhaustive list of skills, efforts, duties, responsibilities or working conditions associated with the position.
Ultralife Corporation is an Equal Opportunity Employer, and as such affirms the right of every person to participate in all aspects of employment without regard to race, color, religion, sexual orientation, gender identity, national origin, citizenship, sex, age, veteran status, disability, genetic information, or any other protected characteristic. If you are interested in applying for employment and need special assistance or an accommodation to apply for a posted position, contact our Human Resources department via phone at 315- 332-7100