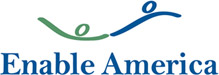
Job Information
Bristol Myers Squibb Sr. Parenteral Manufacturing Technician in Manati, Puerto Rico
Working with Us
Challenging. Meaningful. Life-changing. Those aren't words that are usually associated with a job. But working at Bristol Myers Squibb is anything but usual. Here, uniquely interesting work happens every day, in every department. From optimizing a production line to the latest breakthroughs in cell therapy, this is work that transforms the lives of patients, and the careers of those who do it. You'll get the chance to grow and thrive through opportunities uncommon in scale and scope, alongside high-achieving teams rich in diversity. Take your career farther than you thought possible.
Bristol Myers Squibb recognizes the importance of balance and flexibility in our work environment. We offer a wide variety of competitive benefits, services and programs that provide our employees with the resources to pursue their goals, both at work and in their personal lives. Read more: careers.bms.com/working-with-us .
MAJOR DUTIES AND RESPONSIBILITIES
State the most important activities and accountabilities of this position. Describe how these activities and accountabilities can influence the achievement of departmental or business goals. (Attach additional sheets if needed): Perform mechanical evaluation and troubleshooting
Performs initial evaluation and minor troubleshooting diagnosis of manufacturing equipment failures
Supports maintenance personnel in major troubleshooting diagnosis activities.
Performs complex and highly technical manufacturing operations of aseptic processing and/or isolator technology such as Diafiltration and Concentration of Proteins, Formulation of Proteins, Filling of Proteins in syringes and Vials within Isolators / Barrier Systems or in aseptic area process, Lyophilization process with Automatic Loading within Isolators / Barrier Systems or loading Lyophilizers on aseptic environment, Clean in Place (CIP) and Steam in Place (SIP) process in different systems, Decontamination of Isolator/ Barrier System with Vapor Hydrogen Peroxide (VHP), Sterilization cycles with Steam Autoclaves and Dry Heat Ovens and Tunnels, Isolators and gloves leak test.
Operates in an efficient manner of the manufacturing processes to maximize product yield of products.
Monitors critical process parameters and proactively takes necessary action to prevent process deviation and/or product losses.
Maintains housekeeping within controls and aseptic environments, according to procedures.
Handle Hazardous and Non hazardous waste according to EHS procedures.
Receives, verifies and maintains all production records and transaction documents error free and in compliance with established procedures including computer generate transactions.
Receives, handle, verifies and weights excipients, drug substances, and/or active ingredients.
Performs systems integrity test such as isolators, ultra filtration skid, distribution systems, filters and gloves as required.
Verify calibration status of critical instruments before process operation.
Complete production documentation legible, error free and on time following good documentation practices.
Performs other duties to support other functional areas such as:
Assist manufacturing activities in other areas within operations as required.
Initiates, participates, and assists in resolution of quality investigations.
Audits batch records and documentation, as required.
Revises and improves procedures and develops new SOPs based on observations and experiences.
Participates in special projects, during audits and regulatory inspections as required.
Participates and assists in area validation and qualification activities.
Supports the Annual Requalification Program by assuring plan execution on established timeframe
Attends to all mandatory training meetings for cGMP's, EHS and Company Policies.
KNOWLEDGE/ EDUCATION/ EXPERIENCE:
Describe the knowledge, which is required to perform this job in a satisfactory manner. If this knowledge can be obtained through formal training / education and experience, list the type and amount of education and experience, list the type and amount of education and experience that would typically prepare an individual for this position.
Associate degree in a technical field with seven (7) years of experience in the pharmaceutical field or, Bachelor Degree with five (5) years experience in a Parenteral Manufacturing /Finishing in the Pharmaceutical Industry or Isolation technology.
Basic writing skills when completing area documentation.
Ability to troubleshoot equipment problems and provide resolutions using appropriate problem solving methodology.
Basic knowledge on Computerized, PLC control equipment, procedures and new scientific processes and how to troubleshoot them.
Ability to work with minimum supervision.
Ability to provide job training, theoretical and/or On the Job, for new employees following the Parenteral Operations Department Qualification Curriculum.
Knowledge on critical process parameters and their impact in product quality.
Knowledge in steam sterilization, depyrogenation, filtration sterilization, lyophilization and isolators technology.
Understanding of Process Equipment set-up and able to perform it repeatedly and according to SOPs.
Ability to apply critical thinking to resolve complex issues and day-to-day situations.
Excellent leadership characteristics, accountability and commitment.
Ability to read, write, comprehend detailed technical information and directions and read procedures and documents in English/Spanish Text (e.g. SOPs, Batch Records, etc.)
Team player and collaborating skills.
Knowledgeable in cGMP's, process area, documentation, safety, EHS and hygiene practices.
Functional and basic technical knowledge of complex and automated equipment (computer, or PLC control) for set-up, operation and troubleshoot using the interface systems.
Skill in performing detailed tasks and documenting information.
Ability to enter data into a computer and perform complex process transactions.
Skill in accurate visual inspection (e.g. product and components defects)
Skill in basic mathematical applications.
Skill in navigating through and performing transactions in mfg. computer systems (HMI, hand held computers).
Ability to relate and convert from metric (S.I.) to/from English units.
Ability to plan and/or follows work schedules, set priorities
Strong organizational skills
Able to wear sterile gowns, mask, and full face respirators and able to use Full Face Mask, Latex/Nitrile Gloves, and disposable uniforms on a daily basis.
Willing to work irregular hours, rotative shifts, weekends and holidays when necessary
Ability to operate pallet jacks
CONCENTRATION AND VISUAL EFFORT Describe the extent to which the job requires close attention to detail, and the duration and frequency of projects requiring close concentration:
The incumbent requires a special concentration in several operations activities such as : Working with Isolators, testing activities , weighing activities, equipment set up , troubleshooting, process calculations , gowning and aseptic techniques on aseptic environment, Lyophilization process, Formulation Process, etc.
Demonstrates the attention of each process step on the whole operation. Understand and can explain process flow, sequence and his role and impact within the product manufacturing cycle.
INITIATIVE AND INGENUITY: Describe the responsibility for taking independent action to perform the job, exercising judgment, or devising new methods and procedures for achieving work goals. (Indicate frequency also).
Plan and/or follows work schedules, set priorities with a sense of urgency and meet deadlines in a rapidly changing environment.
Solve day-to-day situations that arise, generates alternatives and evaluates risk vs. benefits aligning personal, team and/or departmental activities with organizational goals and business strategies.
PHYSICAL DEMANDS: Describe job requirements, which induce physical fatigue by means of exertion required. Comment on the frequency and the purpose of activities.
Use hands for scrubbing and gowning procedures.
Wear sterile gowns, mask, and full face respirators where required.
Heavy work requiring to life 25-60 pounds
Requires eye - hand coordination and moving about capacity.
Requires movements of objects such as lifting, carrying, pushing and pulling. It involves body movements such as handling and fingering.
Operators perform the set up and operational activities through gloves in the Isolators.
Use Full Face Mask, Latex/Nitrile Gloves, and disposable uniforms on a daily basis.
The position is under the medical surveillance program
Work irregular hours, rotative shifts, weekends and holidays when necessary. 10. Operate pallet jacks.
RESPONSIBILITY: Describe the kind of job requirements for preventing loss such as:
EQUIPMENT OR PROCESSES:
• Understanding of different process equipment set-up and able to perform it repeatedly.
• Basic mechanical and electronic skills
MATERIAL OR PRODUCT:
• Follows internal procedures when handling processes or equipment and verifies that the Formulation, Filling, Lyophilization, Isolators/processes are executed according with the established parameters.
• The impact of not executing the task in proper form could result on deviation or lot rejection. This impact is based on what part of the process was executed incorrectly.
SAFETY OF OTHERS:
• Able to have quick response in order to handle emergencies.
• The employee must follow safety rules of the area all the time. RESPONSIBILITY FOR WORK OF OTHERS: Generally in Group Leader Positions jobs or where leading Informal or temporary teams is expected).
• Is not responsible for work of others
• Provide support in the coordination of daily activities with the other members of the group.
WORKING CONDITIONS / HAZARDS: Describe the extent to which the job must be performed under working conditions that are considered undesirable, potentially hazardous, require travel, or require absence from home overnight.
Potential exposure to hazardous chemicals substances during plant work.
The incumbent must be trained in waste management disposable procedures.
The use of: hair covers, gloves, coverall suits, respirators, air hoods, ear protection, helmet, etc. for personal and product safety are required accordingly to area that was assigned. Use this space to provide any additional information that you believe would help in evaluating this job.
#BMSBL
#LI-Onsite
If you come across a role that intrigues you but doesn't perfectly line up with your resume, we encourage you to apply anyway. You could be one step away from work that will transform your life and career.
Uniquely Interesting Work, Life-changing Careers
With a single vision as inspiring as Transforming patients' lives through science™ , every BMS employee plays an integral role in work that goes far beyond ordinary. Each of us is empowered to apply our individual talents and unique perspectives in an inclusive culture, promoting diversity in clinical trials, while our shared values of passion, innovation, urgency, accountability, inclusion and integrity bring out the highest potential of each of our colleagues.
On-site Protocol
BMS has a diverse occupancy structure that determines where an employee is required to conduct their work. This structure includes site-essential, site-by-design, field-based and remote-by-design jobs. The occupancy type that you are assigned is determined by the nature and responsibilities of your role:
Site-essential roles require 100% of shifts onsite at your assigned facility. Site-by-design roles may be eligible for a hybrid work model with at least 50% onsite at your assigned facility. For these roles, onsite presence is considered an essential job function and is critical to collaboration, innovation, productivity, and a positive Company culture. For field-based and remote-by-design roles the ability to physically travel to visit customers, patients or business partners and to attend meetings on behalf of BMS as directed is an essential job function.
BMS is dedicated to ensuring that people with disabilities can excel through a transparent recruitment process, reasonable workplace accommodations/adjustments and ongoing support in their roles. Applicants can request a reasonable workplace accommodation/adjustment prior to accepting a job offer. If you require reasonable accommodations/adjustments in completing this application, or in any part of the recruitment process, direct your inquiries to adastaffingsupport@bms.com . Visit careers.bms.com/ eeo -accessibility to access our complete Equal Employment Opportunity statement.
BMS cares about your well-being and the well-being of our staff, customers, patients, and communities. As a result, the Company strongly recommends that all employees be fully vaccinated for Covid-19 and keep up to date with Covid-19 boosters.
BMS will consider for employment qualified applicants with arrest and conviction records, pursuant to applicable laws in your area.
Any data processed in connection with role applications will be treated in accordance with applicable data privacy policies and regulations.
Company: Bristol-Myers Squibb
Req Number: R1580539
Updated: 2024-05-03 04:15:16.345 UTC
Location: Manati-PR
Bristol Myers Squibb is an equal opportunity employer. Qualified applicants will receive consideration for employment without regard to race, color, religion, sex, sexual orientation, gender identity, national origin, age, disability, protected veteran status, pregnancy, citizenship, marital status, gender expression, genetic information, political affiliation, or any other characteristic protected by law.
Bristol Myers Squibb
-
- Bristol Myers Squibb Jobs