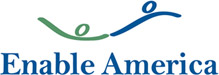
Job Information
Advanced Atomization Technologies Manufacturing Engineer (LP2) in Clyde, New York
FOR INTERNAL USE ONLY
Position: Manufacturing Engineering
Grade: LP2
EEOC Classification: Professionals
FLSA Status: Exempt
Location: Clyde, NY 14433
About Advanced Atomization Technologies
Advanced Atomization Technologies (AA TECH) is a joint venture between Parker Aerospace and GE Aviation, created to produce and support advanced fuel nozzles and related products for current and future commercial engine platforms, including aerospace and aero-derivative engines. The highly skilled and experienced team of AA TECH employees is expert in design, assembly, testing, and aftermarket support, providing our customers with a world-class product and support experience.
AA TECH offers a comprehensive and competitive compensation and benefits package, including:
Variable Incentive Plan (Bonus Eligibility)
Health, Dental, and Vision Insurance with HSA Company Contribution
401k Plan with Employer Match
Tuition Reimbursement
12 Paid Holidays
Vacation Accrual
Position Summary:
A Lead Professional 2 – Manufacturing Engineering is an experienced manufacturing engineer (approximately 6-10 years engineering experience) that will heavily influence the technical direction of the assigned value stream. The successful candidate will be responsible for the operational excellence and success of an assigned value stream which will come from leading continuous improvement efforts, maintaining Value Stream health, and establishing strong working relationships with teammates, engineering leadership and operational leadership.
Key Responsibilities:
Participation in the Technical Support for assigned value stream
Participates/owns in the achievement of the High-Performance Value Stream metrics and initiatives
Participates in the execution of the Strategy Deployment initiative
Participates/owns in process development, documentation, and support
Participates/owns in the assurance of the health of the value stream (FTY, scrap, MDR Onset, TPM)
Inventory management support (MSS, Solumina, Comp Cards)
Problem Solving (RCCA, PDCA, Shainin, etc)
Operational training support
Participation/ownership in the Technical Compliance for assigned value stream
AS13100 Support and Execution
Process / Product Correlation
Process Engineering Change Order process
Metallurgical qualification and compliance (ES6-26 process)
Returned Goods process
Participation/ownership in the Technical support for Lean / Continuous Improvement
Value Stream Mapping
Process Capability Analysis
Process Optimization Data Analysis
Process Mistake Proofing (Identification and implementation)
Participation/ownership in the Technical support for Environmental Health and Safety
Facilitate and support the performing of ergonomic assessments on processes
Facilitate, lead, and support the implementation of ergonomic improvement projects
Ownership of machine safety for all equipment within the value stream
Value Stream Strategy Deployment
Technical support of the long-term strategy
Technical support of the short term AOP Project Identification
Technical support of the Annual SD Project Execution
Talent Development execution for team members (Mfg Eng Techs, Mfg Eng I, Mfg Eng II)
Facilitation of training opportunities and direction
Mentoring technical resources for assigned value stream
Mentoring technical resources for the engineering team
Required Qualifications:
Bachelor’s degree (BS) in Manufacturing Engineering or related engineering field.
6+ years engineering experience or equivalent in a manufacturing environment
Basic knowledge of manufacturing processes, principles and concepts
Basic knowledge of lean principles for manufacturing
Basic knowledge of quality principles for manufacturing
Read and understand GD&T requirements of product drawings
Understand process capability theory
Familiarity with joining processes (braze, weld, etc.)
CAD modeling and drafting experience
Basic blueprint reading and interpretation
Strong mechanical aptitude
Ability to interface with multiple levels of the organization
Effective communication skills: verbal and written
Ability to function in a team environment
Ability to use Microsoft software programs (i.e. Word, Excel, PowerPoint)
Desired Qualifications:
Experience working in cross-functional teams
Experience working with supply chain
Minitab or equivalent stat software
CREO and/or Unigraphics modeling software experience
Six Sigma experience or certification
Due to the Company’s military contractor status, the applicant must be a U.S. citizen or a permanent resident of the United States and must provide evidence of citizenship or immigration status upon applying for the position. Advanced Atomization Technologies, LLC is an equal opportunity employer and gives consideration for employment to qualified applicants without regard to race, color, religion, sex, sexual orientation, age, national origin, disability, protected veteran status, or any other consideration made unlawful by federal, state or local laws. ("Minority/Female/Disability/Veteran/VEVRAA Federal Contractor”)
Typical Mental and Physical Demands:
While performing the duties of this job, the employee may be required to sit. The employee frequently is required to use hands to operate a computer. The employee is occasionally required to stand and walk. Specific vision abilities required by this job include close vision. Also expected of the employee is regular attendance, the ability to work cooperatively and professionally with others and members of the public, and the ability to manage multiple tasks at once.
(The essential functions have been provided as examples of types of work performed by employees assigned to this job classification. The Company reserves the right to modify the work assignments and/or to make reasonable accommodations so that qualified employees can perform the essential functions of the job. The physical and mental demands described above are representative of those required to successfully perform the essential functions of this job.)